Blog 3 Common Types of Sand Used in Sand Casting
Sand casting is a versatile and cost-effective solution for the creation of metal parts. In fact, most metal components can be manufactured using the sand casting method. Sometimes called sand mold casting, sand casting is a great process for small or large-volume orders.
To learn more about the various steps of sand casting process, check out our complete guide of how sand casting is operationally completed from start to finish. This article focusses on the three common types of sand used: green sand, water glass or sodium silicate, and resin sand.
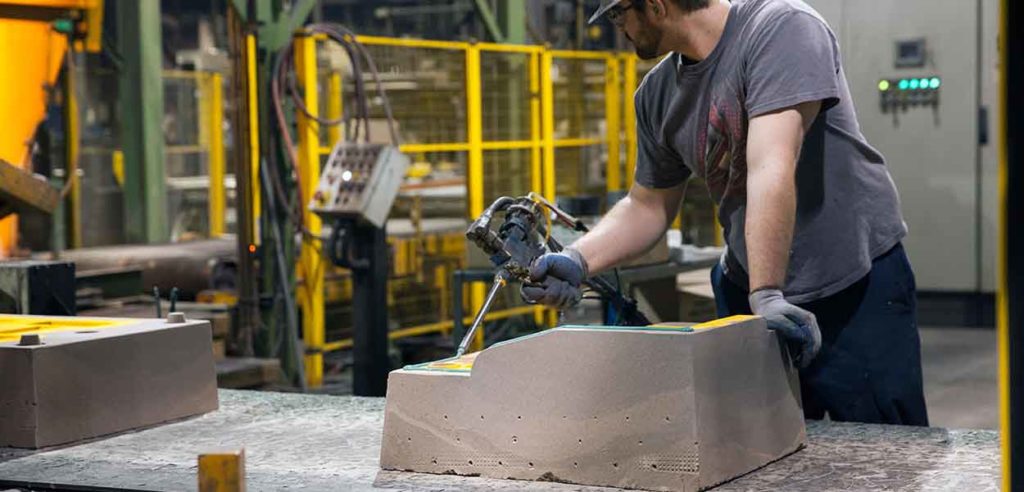
Sand Type One: Green Sand
Green sand isn’t actually green in color but refers to being uncured or essentially raw. Green sand molds are sand combined with water and bonding compounds to produce what is essentially clay. This type of sand is easily reused, which translates to lower costs. It is straightforward to create the molds for casting. However, risk comes into play due to the malleable nature of green sand. Molds can collapse or break during the casting process, but efficiency, continued use of this method, and price points make it a popular choice for sand casting projects.
Sand Type Two: Water Glass or Sodium Silicate
Water glass or sodium silicate is great in casting applications that require a cavity.
Sodium silicate provides a quality mold that allows for higher tolerances. Parts with increased complexity, cavities, dimensional needs, and fantastic surface finish specifications make for a great fit. Water glass requires a mixture of ingredients to ensure the core can break down. Otherwise, it can become stuck inside. The entire project is submerged in hot water to remove the casting mold. It then melts away and can be scooped and reused for future projects. The ability to recycle and cheaper materials make it another excellent casting method in terms of cost, time, and finishing needs. Water glass or sodium silicate is trendy in China but not as common in other countries.
Sand Type Three: Furan Resin Sand
Furan resin sand is the third most common type of sand casting material. A resin mold comprises quartz sand and resin sand. When mixed and heated, resin sand hardens into a durable, smooth mold. The likelihood of a casting breaking down is greatly diminished, but it comes with a higher price point and lead time. Furan resin sand molds are more labor intensive since they must be mixed and heated individually. This is not a quick method of casting. Resin sand, like green sand and water glass, can be recycled for future projects. Resin sand molds are great for smaller production runs and metal projects with many technical specifications needed.
Like any metal casting project, there are several options available. Sand casting is a great option when tooling cost and lead time are leading factors. Green sand is the quickest and most efficient method, followed by water glass or sodium silicate casting. Furan resin sand is a balance between both offering higher dimensional tolerances in the initial cast but trading off for time and money. MetalTek experts are here to work with you each step of the way on your next metal project. Feel free to contact us today.