Turbine Engine
High-Integrity Components For The Flight And Land-Based Turbine Engine Industry
In the turbine engine market, quality is not compromised. Our flight turbine engine products do not just have to meet high standards; they simply can never fail. MetalTek has decades of experience delivering quality components that keep travelers safe. The reliability of our manufacturing processes has made MetalTek a leading supplier of compressor cases on many of the world’s most successful flight turbine engine programs. Our applications range from high bypass turbofan engines and jet engines to marine power and mechanical drives. Explore more of MetalTek’s applications and engine products below.
Land-based turbine customers producing large, tight-tolerance systems confront multiple stresses and elevated temperatures. MetalTek has unique shaping capabilities that help us deliver significant long-term cost savings compared to other manufacturing processes for these power generation applications. We combine this with the material integrity of the centrifugal process to deliver exceptional value to customers.
With a legacy spanning nearly half a century, MetalTek has been a trusted and reliable casting solutions provider for flight and land-based turbine engines.
Turbine Engine Market Video
Typical Turbine Engine Products
-
Bearing supports
-
Combustor cases
-
Combustor hardware
-
Compressor cases
-
Exhaust diffusers
-
Fan cases
-
Fuel system components
-
Mandrels and forming dies
-
Stationary inlet guides
Typical Turbine Engine Applications
-
Auxiliary power generation
-
High bypass turbofan engines
-
Jet engines
-
Marine power
-
Mechanical drives
-
Turboprop engines
Certifications and Compliance
-
ISO 9001:2015 (QMS)
-
AS9100D (QMS)
-
Nadcap (non-destructive testing)
-
Nadcap (laboratory testing)
-
Nadcap (heat treating)
-
Nadcap (in-process welding)
Need help with a new project?
Let's push the limits of what is possible, together. Ask your metal experts.
Solutions
We are dedicated to the turbine engine market to ensure that customers get the technical expertise, quality, and reliability they deserve. Explore a selection of our top solutions for the turbine engine industry.
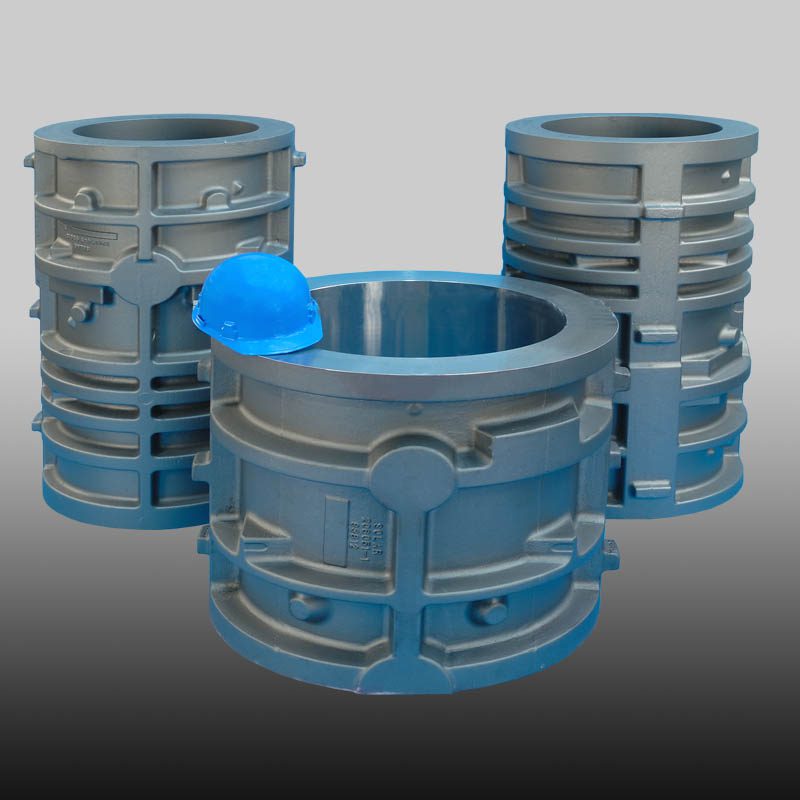
Near-Net Shaped Turbine Engine Cases
Near-net centrifugals are the most cost effective solution for heavy wall cases.
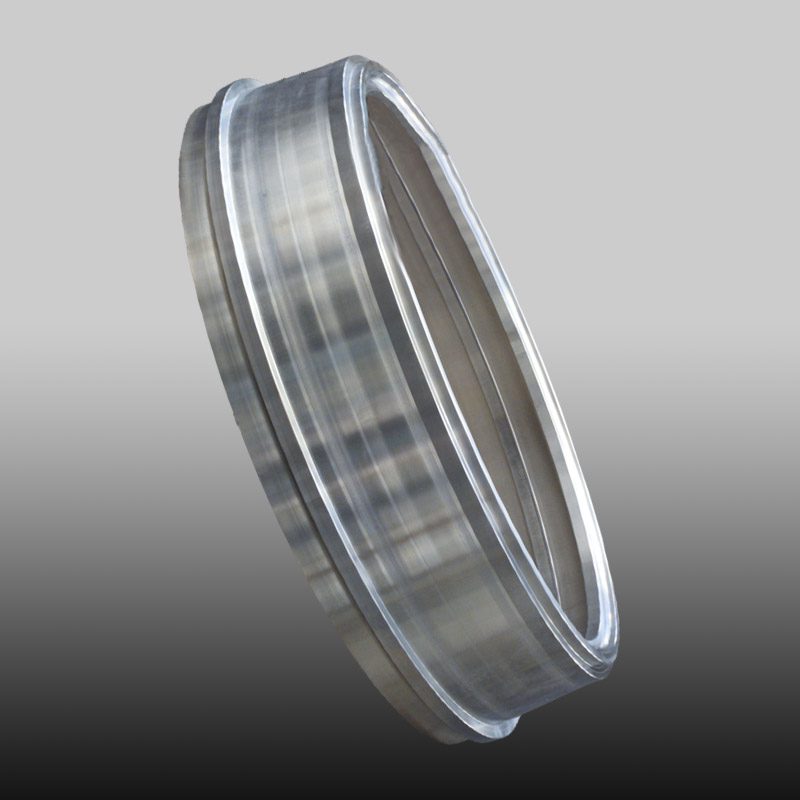
Tooling Mandrel
Centrifugally cast tooling can provide 5 times longer tool life than traditional fabricated assemblies.