Blog Tooling for Different Types of Casting Processes
By: Jason Kay
Tooling is critical to the different metal casting processes that MetalTek uses to manufacture components for the world’s most demanding industries such as aerospace, defense, and petrochemical. Our metal castings must be efficient, precise, and innovative. They simply cannot fail – even in high-heat, high-wear, and high-corrosion environments.
Metal casting involves pouring molten metal into a mold to create a part or component. Tooling helps create the mold, which can be permanent, an expendable or perishable mold that is used once, or a combination of multiple mold technologies (depending on the process). Metal casting can be dangerous, but MetalTek believes every job can be done safely by following procedures and by casting with the proper tooling, engineered controls, and related equipment.
Read on to learn about how tooling differs for each of our casting processes.
The Most-Used Methods of Casting at MetalTek:
Centrifugal Casting involves molten metal poured into a spinning mold (also known as a die in centrifugal casting). This mold rotates on a vertical axis or horizontal axis, depending on the part configuration. Centrifugal force acts on the molten metal in the rotating mold, causing impurities in the metal to float to the center due to high velocity.

Sand Casting is a versatile casting method where a pattern of the finished part is created from wood, foam, urethane, or metal. Sand fortified with a bonding material is packed around this pattern. The pattern is then separated from the sand, leaving a cavity into which the part will be shaped when the molten liquid metal is added.
Investment Casting is a static casting process like sand casting but instead uses a wax pattern of the finished part. The pattern is created by injecting molten wax into a pattern tool. This pattern is then attached to a wax “tree” that is dipped into a ceramic slurry and stucco material and then allowed to dry. The wax dipping is repeated until a shell forms over the wax pattern. The wax pattern is melted away, and molten metal is poured into the shell to form the part.
Each of these casting processes require tooling. The process of designing tools and the tools themselves vary by process and the requirements of the final part to be manufactured.
The Different Types of Tooling for Casting Processes:
In metal casting tooling is used to produce the molds into which molten metal is poured to create the cast part. Molds are permanent or expendable, depending on whether they are reused. At MetalTek permanent molds are primarily used in centrifugal casting. Molten metal comes in direct contact with permanent molds (dies), which are durable and reusable. MetalTek’s Wisconsin Centrifugal Division maintains the largest centrifugal die inventory in the world, which can significantly lower upfront costs for customers.
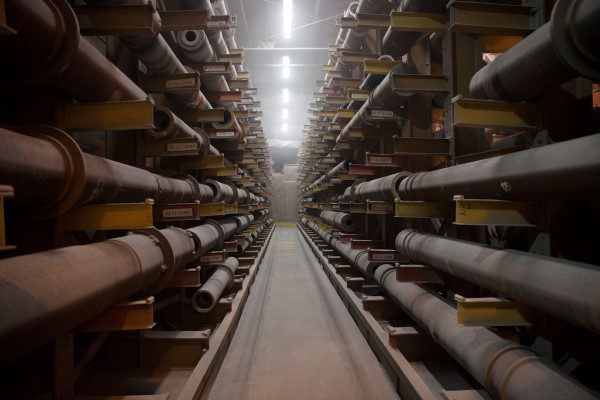
Molds used in sand casting and investment casting are expendable and cannot be reused. The sand-casting process starts with a pattern of the part to be cast. This pattern is the tool and is used to create the sand mold into which molten metal is poured. The sand must be removed to access the cast part. In investment casting the pattern tool has a cavity that is the negative of the part to be cast. The tool is injected with wax to create the pattern, which is ultimately melted from its hardened shell to create the mold. The mold is removed after casting, leaving the part.

at MetalTek’s Carondelet Division

Using current advanced manufacturing technology, it is possible to create an expendable mold without a tool. Both additive and subtractive techniques can create a mold with the geometry coming from a solid model. This mold is destroyed when the casting is removed but can be created from the digital geometry of the part to be cast.
Understanding the intended application, alloy, and annual usage for a specific part starts the design process for a given tool. Since metal parts often work in conjunction with other components, it is imperative that they are precisely sized and shaped.
Why is Dimensional Accuracy in Tooling Important?
The quality of the surface determines its function, performance, and durability. For example, sand casting generally produces rougher as-cast surface than investment casting because of the characteristics of the mold. Alternatively, the ceramic slurry used in investment casting results in a finer, tighter surface and better geometric performance.
Tooling wear can cause the dimensions of the casting itself to start to shift which triggers a total reworking of the tool. Process control is managed by a pre-and-post inspection. This inspection can be of critical dimensions or surfaces on the castings themselves, inspection of the tooling (or both) and depends on the casting technology used, the material of the tooling, and the number uses the tool has seen.
How Does MetalTek Stand Apart in the Tooling Process?
Metal casting process variability can be a perceived disadvantage compared to competing manufacturing methods. Metal casting companies may need to prepare for some back-and-forth with machining part requirements and the functional surfaces that determine where and when machining is needed. However, with variation comes opportunity. The geometry that can be accommodated using an optimized tooling package is vast, including geometries that are internal or cannot to be created with other methods of manufacturing such as forging or machining.
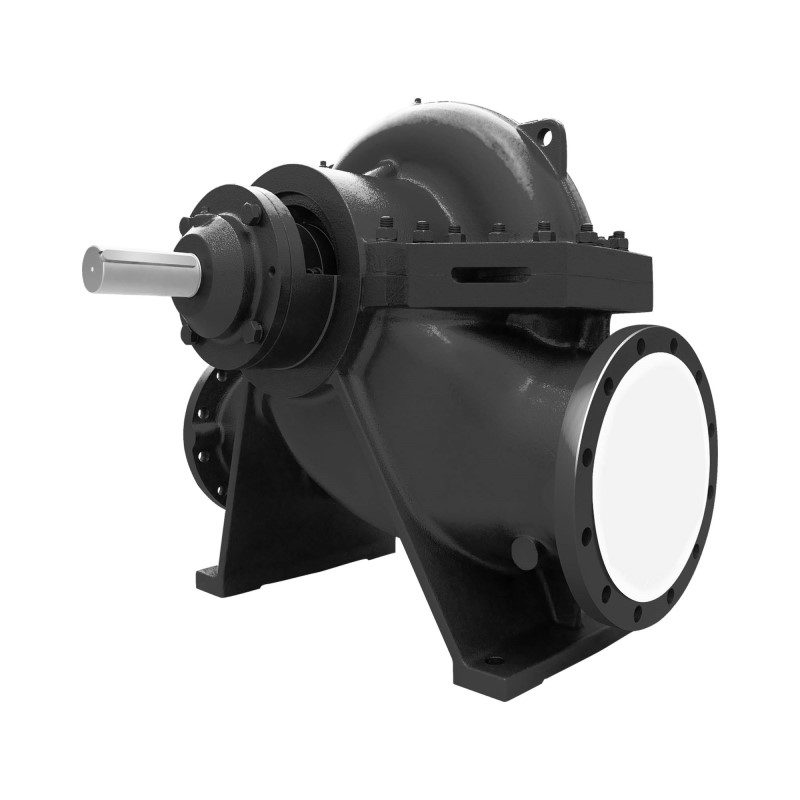
When compared to machining parts from raw stock or bar, casting can have many advantages. The geometry created by the tooling displaces material that would otherwise need to be machined away. Detail of some components can often only be created using the metal casting process. A prominent example of this are castings made for pumps. The lower half of the pump case is a sand casting because it is a large, heavy-duty part that holds the bearings and drive. The impeller can be made as an investment casting so the internal surfaces (the working part of the pump) contain finer detail and better hydraulics, and can function better with smoother, performance related enhancements.
Any metal can be melted, mixed, or made available to be cast. The time casting and tooling take to be created can vary by process or capacity. MetalTek is not a captive foundry for a large OEM with a made-to-stock product line. We produce critical metal components to exact specifications for thousands of customers in demanding industries. MetalTek starts the clock when a custom order arrives, and castings can take as little as weeks to more than a year depending on their complexity. MetalTek partners with customers to find solutions that fits their needs, and we thrive because of our ability to find solutions for a rare alloy, challenging geometry, or a unique application.
Changing Trends in Casting Technology
The current trends in advanced manufacturing do have application to the legacy casting processes. More and more engineers are turning to digital manufacturing, where a digital file or a 3D model of a part can be used to create a pattern or a mold using rapid prototype technologies: 3D printing, stereolithography (SLA), or machining a cavity, all reliant on new technology. Directly printing these patterns, coupled with traditional casting process can help meet the customer demands. If a complex pattern is lost or needs to be replicated, it is easily accessed in a digital file.
This digital future of casting means a wider variety of sizes of parts can be made without a hard tool. Though it will be some time until the technology is scalable to larger parts, the additive manufacturing industry is growing at an exponential rate and there could be a shift to additive manufacturing as the primary manufacturing process for tooling and molds used for metal castings.
The application of additive manufacturing technologies and processes to metal casting is an area of limitless possibility. MetalTek’s commitment to safety, innovation, and expertise in casting and tooling ensure we will be both the forerunner to new technologies and a mainstay in process management in metal manufacturing.
About the Author
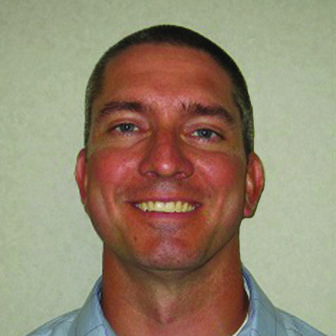
Jason Kay is Sales Manager for the Eastern U.S. and Canada at MetalTek International. He joined MetalTek in 2003 and has served in field sales, inside sales, and continuous improvement roles. Jason holds a Bachelor of Science Degree in Mechanical Engineering from the University of Wisconsin-Milwaukee.