Blog What to Consider in Metal Casting Design
By: Mike McCleary and Calvin Rose
From large projects to small production runs, selecting the appropriate metal casting process to achieve the desired design can be difficult. MetalTek focuses on three primary metal casting processes: centrifugal casting, sand casting, and investment casting. Each comes with numerous design considerations ranging from overall shape to surface finish to dimensional tolerance. This article focuses on reviewing each metal casting process and then outlining top design factors that customers should understand as they begin a project. Regardless of the metal casting process, MetalTek helps customers achieve their desired casting designs.
Metal Casting Processes
Dynamic Casting Methods:
Dynamic casting refers to metal casting processes where the mold moves during the introduction of molten metal.
Centrifugal Casting
Centrifugal casting is a dynamic casting method best suited to produce round, symmetrical parts that are rings, sleeves, or tubes. Like sand castings, centrifugal castings are available in a wide range of sizes and can exceed 100,000 pounds. The centrifugal casting process can be more cost-effective than other processes as it has reduced machining requirements and lower manufacturing costs.
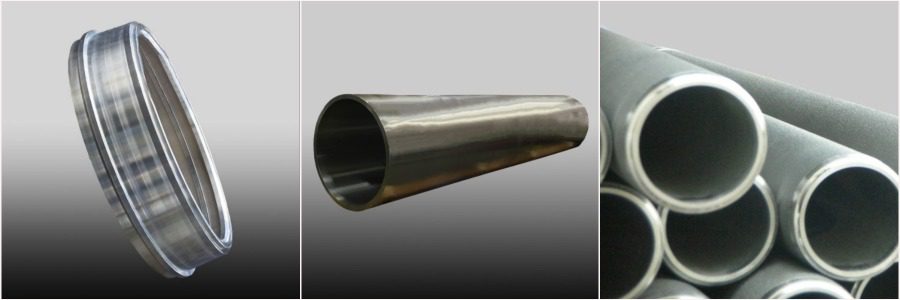
Centrifugal casting begins with molten metal poured into a heated, rapidly spinning die. Centrifugal force created by the spinning of the die distributes metal equally toward the outside diameter (OD) and causes lighter material (oxides and other impurities) to migrate toward the inside diameter (ID). Metal solidifies from the OD towards the ID, leaving the purest metal on the outside of the casting and pushing the less pure elements toward the center. Machining removes impurities from the ID, resulting in a casting of the highest quality.
Static Casting Methods:
Static casting refers to metal casting processes where the mold does not move during the introduction of molten metal.
Sand Casting
Sand casting, or sand molded casting, is a metal casting process that uses sand as the mold material. As the oldest casting method and perhaps the most versatile, sand casting is widely used in a variety of applications. Parts that fit well with this process generally have external shaping and internal passageways and can weigh from a pound to tens of thousands of pounds.
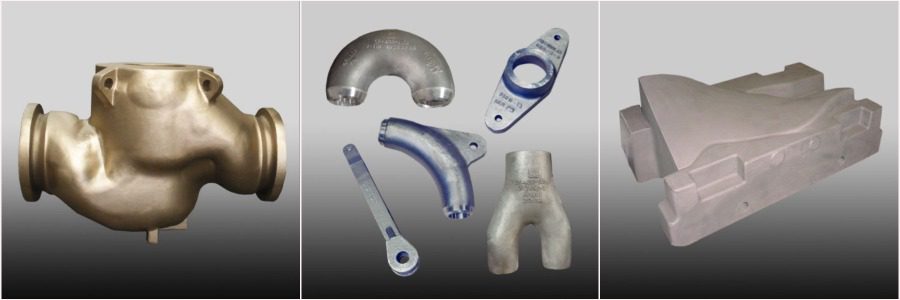
The sand-casting process begins with a pattern (typically hardwood, polyurethane, or another durable material) shaped like the final part. This pattern is surrounded by a sand mold and then removed, leaving a cavity in the shape of the part within the sand mold. Molten metal is poured into the cavity using hollow pathways called risers and runners. After metal solidification, risers and runners are removed. This leaves a metal part in the shape of the pattern. 3D printing technology can be used to replace patterns made with the traditional materials.
Investment Casting
The investment casting process produces shaped or non-symmetrical parts with internal passageways and extremely fine detail and surface finish. With such fine finishes machining, labor, and material costs are reduced. Investment casting is ideal for lower-weight parts of approximately 1,000 pounds or less. If a project has unique geometries and tight dimensional tolerances, investment casting is likely the best fit.
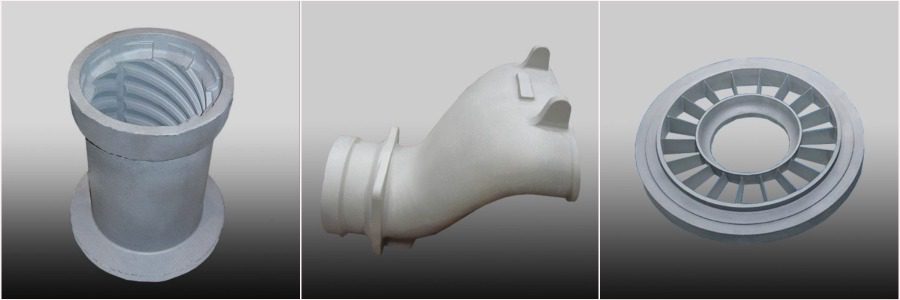
Investment casting begins with a wax pattern that is identical to the final shape of the part. The pattern is covered by multiple layers of a ceramic slurry. After hardening, the wax is melted away to create a hollow mold of the part into which liquid metal is poured. After metal solidification a shakeout process occurs, and the final part remains. Investment castings can also be produced using stereolithography (SLA). In SLA a 3D printed pattern replaces the traditional wax pattern and the need for hard tooling.
Metal Casting Design Considerations
Now that we described MetalTek’s main metal casting processes, we will review the primary design considerations for metal casting. Understanding these considerations helps customers choose the best metal casting processes for their specific applications. Please note that metal casting design is just one consideration when choosing a metal casting process and must be balanced with other factors to meet a customer’s commercial and technical requirements.
Metal Casting Shape
The first metal casting design consideration is shape. If the part is generally round (i.e., a ring, sleeve, or tube) then centrifugal casting is probably the appropriate metal casting process. If the part is not a round shape and has a complex geometry with features such as internal passageways or ribs, then investment casting or sand casting is most appropriate.
The remaining design considerations focus on choosing between investment casting and sand casting.
Metal Casting Size
Sand castings are available in a much greater range of sizes than investment castings. While investment castings produced by MetalTek’s Wisconsin Investcast Division are typically up to 1,200 pounds, sand castings produced by MetalTek’s Carondelet Division range from just a few pounds to 20,000 pounds. If a casting is less than about 1,200 pounds, then the customer must consider the level of detail and overall geometry required to choose between investment casting and sand casting.
Casting quality is supported by solidification modeling software. This software simulates the flow of molten metal into molds and analyzes the predicted solidification as the mold cools. This model supports mold design to ensure a compliant part.
Dimensional Tolerance
Dimensional tolerance refers to the permissible deviation from the desired measurements of a metal casting. Generally, investment casting will achieve tighter tolerances (e.g., +/-0.010” for the first inch and +/- 0.004” for each succeeding inch) than other metal casting methods, even for parts with fine detail and internal passageways. While sand casting will not usually achieve the dimensional tolerance of investment casting, it can offer complex geometries and detail in a much larger overall size.

Surface Finish
Surface finish refers to the external texture of the part after metal casting and is measured by root mean square (RMS). Investment casting generally has a finer (60 to 200 RMS) as-cast surface finish than sand casting (250 RMS or more). This typically results in a reduced need for machining (see below). Sand castings can be machined to achieve a finer surface finish, but this involves additional cost and lead time. If a fine surface finish is not required, sand casting offers complex geometries and detail, often at a lower overall cost than investment casting.
Machining Requirements
Metal casting design must consider the amount of metal from the casting that will be removed by machining to achieve the desired shape and features. Machining can significantly add to cost and lead time. Virtually all components that MetalTek produces are machined to some degree either by MetalTek or by the customer after shipping.
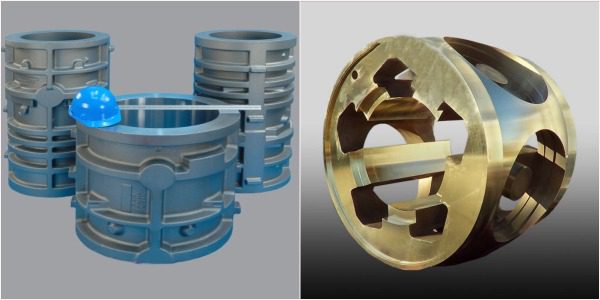
Near net shaping combines centrifugal casting with sand or investment casting, and results in a metal casting that is as close to the final size and shape as possible. This significantly reduces the need for machining. Between the standalone static casting processes, sand casting generally requires more machining than investment casting to achieve comparable surface finish and fine detail.
Shrinkage
Shrinkage refers to the contraction of molten metal during cooling and must be considered to protect casting dimensions and casting integrity. The potential negative effects of shrinkage are:
- Unexpected changes in casting dimensions
- Voids or pockets within the casting wall or surface that threaten casting integrity
Dimensional shrinkage can be calculated for specific alloys and adjusted in the tooling to meet the required dimensional tolerances. Shrinkage is further controlled during investment and sand casting with gating, which is the delivery system of the liquid metal to the mold. Gates also act as “reservoirs” by adding liquid metal to the casting during solidification to achieve a defect-free casting shape.
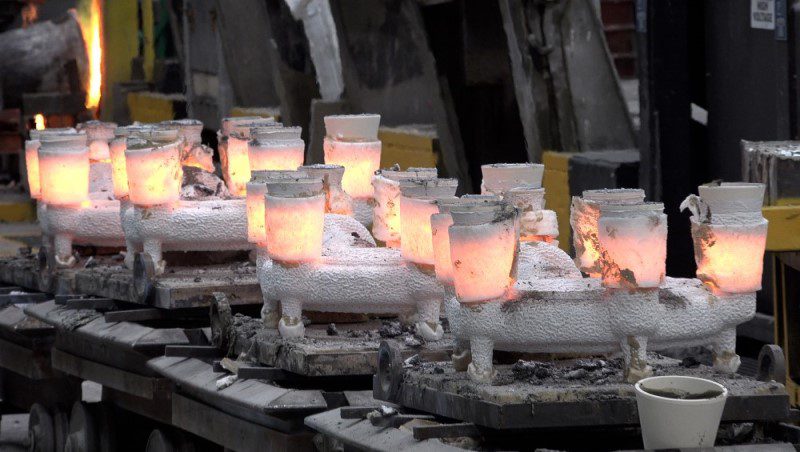
Metal Casting Design: Final Thoughts
Metal casting shape and size are the first two design considerations when choosing the appropriate metal casting process. A round shape such as a ring, tube, or sleeve will almost always be a centrifugal casting. When choosing between investment casting and sand casting, overall size is the first consideration. If a casting is over about 1,200 pounds, then it will most likely be a sand casting. If the overall size is below 1,200 pounds, then the customer must balance design considerations such as surface finish and dimensional tolerance.
Whether centrifugal, investment, or sand casting, MetalTek works with customers to choose the most appropriate metal casting process to meet the specific requirements of their designs. From the selection of the metal casting process to the considerations in that selection, MetalTek focuses on these conversations from the start.
Contact us to learn more.
About the Authors
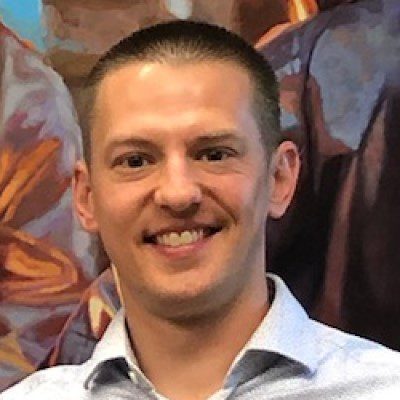
Mike McCleary is Sales Manager for MetalTek’s Wisconsin Investcast Division. He joined MetalTek in 2008 and previously served as Sales Engineer at MetalTek’s Wisconsin Centrifugal Division. Mike holds a BS in Mechanical Engineering from Marquette University.

Calvin Rose is Sales Engineer at MetalTek’s Wisconsin Investcast Division. He has spent over 40 years with Wisconsin Investcast and previously served in Foundry, Finishing, Layout, Liquid Penetrant Inspection, Process Engineering, and Plant Supervision.